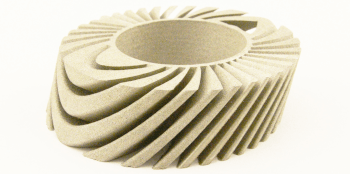
In our recent publication, we showed how to overcome current process limitations in additive manufacturing by segmenting the part on a complex-shaped winding former. The research was a collaboration between ispire AG, ETH Zurich and the Paul Scherrer Institute.
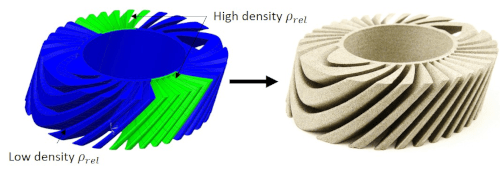
In additive manufacturing (AM), low geometrical tolerances, high-quality material properties, and low surface roughness are challenges.
Instead of selecting identical process parameters to the geometry of the whole part, different sets of process parameters are assigned to different regions named the manufacturing elements approach.
This study shows an end-to-end implementation of the manufacturing elements approach for the fabrication of a complex-shaped winding former of a superconducting solenoid coil. By applying this approach the performance of a solenoid coil can be improved which enables an increased performance e.g. for the future circular collider at CERN and to realize proton beams for accurately treating cancerous tumors.
This approach offers three main advantages: significant reduction of required sacrificial support structures based on the reduced build angles and less post-processing efforts; reduced AM processing time due to less sacrificial support structures and a higher laser speed; and local adjustment of the material and surface properties.
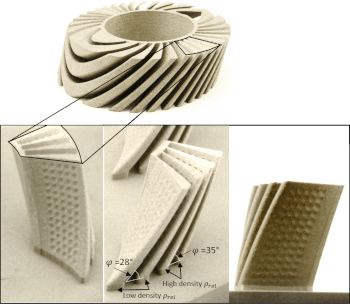